Recognizing Porosity in Welding: Exploring Reasons, Results, and Prevention Strategies
Porosity in welding is a consistent challenge that can significantly impact the quality and integrity of welds. As specialists in the welding sector are well conscious, understanding the reasons, impacts, and avoidance strategies associated to porosity is vital for accomplishing robust and trustworthy welds. By delving right into the source of porosity, analyzing its detrimental results on weld quality, and discovering efficient avoidance techniques, welders can improve their understanding and skills to generate top notch welds regularly. The intricate interaction of factors adding to porosity requires a detailed understanding and a proactive method to make sure effective welding end results.
Usual Sources Of Porosity
Contamination, in the type of dirt, oil, or rust on the welding surface area, creates gas pockets when heated up, leading to porosity in the weld. Improper shielding happens when the securing gas, frequently used in processes like MIG and TIG welding, is not able to fully shield the liquified weld swimming pool from reacting with the bordering air, resulting in gas entrapment and succeeding porosity. Additionally, inadequate gas coverage, typically due to incorrect flow prices or nozzle positioning, can leave parts of the weld vulnerable, allowing porosity to develop.
Impacts on Weld High Quality
The visibility of porosity in a weld can substantially compromise the general quality and integrity of the bonded joint. Porosity within a weld creates voids or tooth cavities that weaken the framework, making it extra susceptible to fracturing, rust, and mechanical failure. These spaces work as stress concentrators, decreasing the load-bearing capability of the weld and enhancing the probability of premature failing under used stress. On top of that, porosity can additionally act as possible websites for hydrogen entrapment, more intensifying the destruction of the weld's mechanical residential or commercial properties.
Moreover, porosity can impede the effectiveness of non-destructive screening (NDT) methods, making it testing to spot various other issues or discontinuities within the weld. This can result in significant safety worries, particularly in critical applications where the structural stability of the welded elements is critical.
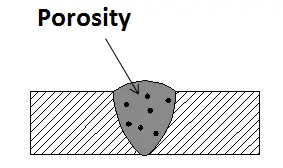
Prevention Techniques Summary
Given the damaging influence of porosity on weld quality, efficient avoidance methods are important to maintaining the structural honesty of welded joints. Additionally, choosing the proper welding specifications, such as voltage, current, and travel rate, can aid decrease the danger of porosity development. By integrating these prevention strategies right Learn More into welding practices, the occurrence of porosity can be considerably minimized, leading to more powerful and much more trustworthy bonded joints.
Value of Proper Protecting
Proper securing in welding plays a crucial function in avoiding climatic contamination and guaranteeing the stability of welded joints. Securing gases, such as argon, helium, or a combination of both, are frequently made use of to secure the weld swimming pool from reacting with components in the air like oxygen and nitrogen. When these responsive elements enter contact with the warm weld pool, they can cause porosity, leading to weak welds with lowered mechanical residential properties.

Inadequate shielding can result in various defects like porosity, spatter, and oxidation, compromising the structural integrity of the welded joint. Adhering to appropriate protecting techniques is vital to produce top quality welds with marginal problems and ensure the longevity and dependability of the bonded parts.
Tracking and Control Techniques
Just how can welders successfully keep track of and regulate the welding process to make sure ideal results and protect against issues like porosity? One trick method is with making use of innovative tracking innovations. These can consist check my site of real-time tracking systems that give responses on criteria such as voltage, current, travel rate, and gas flow rates. By constantly keeping an eye on these variables, welders can determine deviations from the optimal problems and make prompt adjustments to stop porosity development.

Furthermore, carrying out appropriate training programs for welders is important for monitoring and regulating the welding procedure efficiently. What is Porosity. Enlightening welders on the importance of maintaining consistent criteria, such as correct gas shielding and travel speed, can assist avoid porosity issues. Normal evaluations and qualifications can also weblink guarantee that welders are skillful in surveillance and managing welding processes
Moreover, making use of automated welding systems can boost tracking and control capacities. These systems can exactly regulate welding specifications, reducing the probability of human error and making sure consistent weld top quality. By incorporating innovative monitoring modern technologies, training programs, and automated systems, welders can effectively keep track of and regulate the welding procedure to minimize porosity flaws and attain top notch welds.
Conclusion
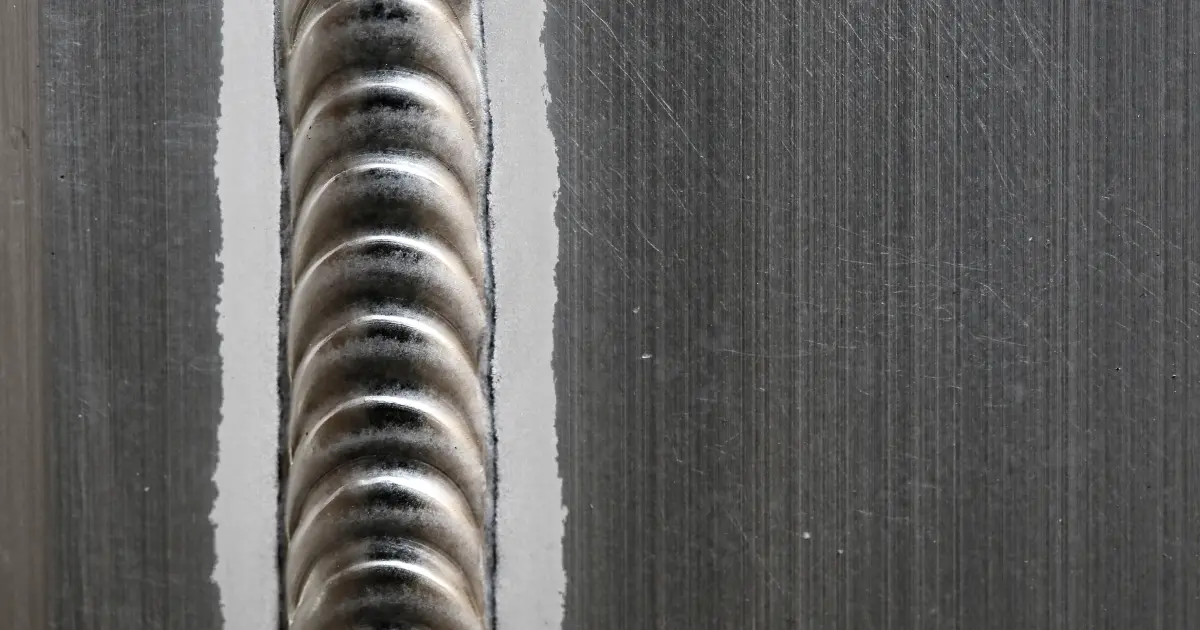
Comments on “Comprehensive Overview: What is Porosity in Welding and Exactly How to avoid It”